Zapas maksymalny – definicja, jak obliczyć, optymalizacja
W logistyce zarządzanie magazynem odgrywa znaczącą rolę w zapewnieniu płynności operacji i optymalizacji kosztów. Jednym z filarów tego procesu jest zapas maksymalny. Choć często pozostaje w cieniu, to właśnie on gwarantuje stabilność i sprawność całego łańcucha dostaw.
Zapas maksymalny to nie tylko liczba produktów, które można zmieścić w magazynie. Jest to przemyślane narzędzie strategiczne, które pozwala firmom znaleźć równowagę między kosztami przechowywania a koniecznością utrzymania ciągłości dostaw. Precyzyjne określenie tego parametru eliminuje ryzyko:
- pustych półek,
- przepełnionych magazynów,
- nieefektywnego zarządzania finansami,
- strat wynikających z niewykorzystanych zasobów.
W rezultacie przedsiębiorstwo skuteczniej zarządza finansami, ogranicza straty i lepiej wykorzystuje dostępne zasoby.
W praktyce zapas maksymalny pełni funkcję bufora, chroniąc firmę przed ryzykiem związanym z:
- nagłymi wzrostami popytu,
- opóźnieniami w dostawach,
- przestojami w produkcji,
- zakłóceniami w sprzedaży.
Jakie korzyści niesie zarządzanie zapasami maksymalnymi?
Efektywne zarządzanie zapasami maksymalnymi przynosi firmie szereg korzyści, takich jak:
- lepsze wykorzystanie przestrzeni magazynowej,
- redukcja kosztów przechowywania,
- zwiększenie elastyczności operacyjnej,
- minimalizacja ryzyka strat finansowych.
Jakie strategie warto wdrożyć?
Aby w pełni zoptymalizować proces zarządzania zapasami maksymalnymi, warto rozważyć następujące strategie obejmujące:
- regularną analizę danych dotyczących popytu i podaży,
- wykorzystanie nowoczesnych systemów zarządzania magazynem (WMS),
- ścisłą współpracę z dostawcami w celu skrócenia czasu realizacji zamówień,
- szkolenia dla pracowników odpowiedzialnych za logistykę.
Odpowiedzi na powyższe pytania mogą okazać się przełomowe dla logistyki w Twojej firmie. Mogą otworzyć nowe perspektywy rozwoju i wynieść efektywność operacyjną na zupełnie nowy poziom.
Czym jest zapas maksymalny? Definicja.
Ale czy wiesz, czym tak naprawdę jest zapas maksymalny? To maksymalna ilość towarów, jaką firma może przechowywać w magazynie, aby uniknąć zbędnych kosztów i strat. Jednak to coś więcej niż tylko liczba – to fundament efektywnego zarządzania magazynem. Dzięki niemu firma może działać sprawnie, nie przepalając budżetu na niepotrzebne wydatki.
Wyobraź sobie zapas maksymalny jako górną granicę – swoisty „stop” dla nadmiaru towarów. Przekroczenie tej granicy może prowadzić do:
- wzrostu kosztów magazynowania, co obciąża budżet firmy,
- utraty wartości produktów, zwłaszcza tych z krótkim terminem ważności,
- nieefektywnego wykorzystania przestrzeni magazynowej.
Dlatego tak istotne jest, aby każda firma precyzyjnie określała swoje zapasy maksymalne, uwzględniając:
- specyfikę branży, w której działa,
- rynek i zmieniające się potrzeby odbiorców,
- sezonowość oraz trendy sprzedażowe.
Odpowiednie zarządzanie zapasem maksymalnym to nie tylko oszczędność, ale także strategia na przyszłość, która pozwala firmie utrzymać stabilność finansową i operacyjną.
Sprawdź również: https://wdx.pl/2020/10/20/zapasy-magazynowe/
Rola zapasów maksymalnych w zarządzaniu łańcuchem dostaw
W całym logistycznym procesie zapas maksymalny odgrywa wręcz strategiczną rolę. To on decyduje, czy firma działa sprawnie i czy klienci otrzymują swoje zamówienia na czas. Dobrze ustalony zapas maksymalny pozwala firmom:
- utrzymać ciągłość dostaw, nawet w obliczu nieprzewidzianych sytuacji,
- unikać problemów związanych z nadmiarem towarów, takich jak marnowanie zasobów,
- minimalizować niepotrzebne koszty operacyjne.
Skuteczne zarządzanie zapasami maksymalnymi to coś więcej niż tylko planowanie. To także:
- synchronizacja działań w całym łańcuchu dostaw,
- większa elastyczność w reagowaniu na zmieniające się potrzeby rynku,
- budowanie silniejszej pozycji konkurencyjnej na rynku.
W efekcie firma zyskuje niższe koszty operacyjne, szybciej reaguje na zmiany oraz osiąga przewagę nad konkurencją.
Czynniki wpływające na ustalanie zapasów maksymalnych
Proces ustalania zapasów maksymalnych wymaga uwzględnienia wielu zmiennych, które decydują o efektywności zarządzania magazynem. Główne składowe to punkt zamawiania, wielkość uzupełnienia, minimalny popyt oraz lead time. Każdy z tych elementów odgrywa istotną rolę w określaniu optymalnej ilości towarów. Celem jest jednoczesne ograniczenie kosztów i zapewnienie ciągłości dostaw. Poniżej omówimy każdy z wymienionych wyżej czynników.
Punkt zamawiania i wielkość uzupełnienia
W logistyce punkt zamawiania oznacza moment, w którym należy złożyć zamówienie na uzupełnienie zapasów. Precyzyjne określenie tego punktu pozwala uniknąć braków magazynowych, jednocześnie utrzymując płynność operacyjną. Natomiast wielkość uzupełnienia to ilość towarów, którą trzeba zamówić, uwzględniając zapas zabezpieczający. Oba te elementy są podstawą przy obliczaniu zapasu maksymalnego, wskazując, kiedy i ile produktów zamówić, by uniknąć nadmiernych kosztów przechowywania oraz zamrożenia kapitału.
- Punkt zamawiania – moment składania zamówienia, by uniknąć braków magazynowych.
- Wielkość uzupełnienia – ilość towarów do zamówienia, uwzględniająca zapas zabezpieczający.
Wyobraźmy sobie firmę sprzedającą elektronikę. Może ona ustalić punkt zamawiania na podstawie średniego dziennego popytu oraz czasu realizacji dostawy. Dzięki temu planowanie staje się bardziej precyzyjne, a ryzyko braków – znacznie mniejsze.
Minimalny popyt i Lead Time
Minimalny popyt to najniższy poziom zapotrzebowania na dany produkt w określonym czasie. Znajomość tego parametru pozwala uniknąć sytuacji, w której zapasy spadają poniżej poziomu krytycznego. Z kolei lead time, czyli czas od złożenia zamówienia do jego realizacji, wpływa na zdolność firmy do szybkiego reagowania na zmieniające się potrzeby rynku.
- Minimalny popyt – najniższy poziom zapotrzebowania w określonym czasie, kluczowy dla uniknięcia krytycznych braków.
- Lead time – czas realizacji zamówienia, wpływający na elastyczność firmy wobec zmian rynkowych.
W branży spożywczej, gdzie lead time wynosi zaledwie kilka dni, minimalny popyt musi być dokładnie oszacowany. Jest to niezbędne, by uniknąć przestojów w dostawach. Oba te czynniki wspierają synchronizację dostaw i minimalizują ryzyko przerw w działalności operacyjnej.
Sezonowość i model konsumpcji
Sezonowość oraz model konsumpcji klientów to kolejne istotne aspekty. Sezonowość odnosi się do okresów wzmożonego popytu, takich jak święta czy sezon wakacyjny. W takich momentach firmy muszą dysponować dodatkowymi zapasami, by sprostać oczekiwaniom rynku. Z kolei analiza modelu konsumpcji, czyli nawyków zakupowych klientów, pozwala lepiej dostosować zapasy do rzeczywistych potrzeb.
- Sezonowość – okresy wzmożonego popytu, np. święta czy sezon wakacyjny, wymagające dodatkowych zapasów.
- Model konsumpcji – analiza nawyków zakupowych klientów, umożliwiająca lepsze dostosowanie zapasów.
Weźmy przykład branży odzieżowej, gdzie trendy zmieniają się błyskawicznie. Zrozumienie preferencji klientów pomaga uniknąć zarówno nadmiaru, jak i niedoboru towarów. Dzięki temu firmy mogą efektywnie zarządzać zapasami, jednocześnie utrzymując konkurencyjność.
Przestrzeń magazynowa i koszty przechowywania
Nie można pominąć kwestii takich jak przestrzeń magazynowa oraz koszty przechowywania. Nadmierne zapasy prowadzą do wzrostu kosztów – wynajem przestrzeni, energia, wynagrodzenia dla personelu – to wszystko się sumuje. Z drugiej strony, ograniczona przestrzeń magazynowa może uniemożliwić przechowywanie większej ilości towarów. Dlatego precyzyjne planowanie jest tutaj absolutnie niezbędne.
- Przestrzeń magazynowa – ograniczona przestrzeń może uniemożliwić przechowywanie większej ilości towarów.
- Koszty przechowywania – nadmierne zapasy generują dodatkowe koszty, takie jak wynajem, energia czy wynagrodzenia.
Jako przykład służy firma logistyczna, która może wdrożyć systemy automatyzacji magazynowej, by lepiej wykorzystać dostępną przestrzeń i zminimalizować koszty operacyjne. Zrozumienie tych czynników pozwala podejmować świadome decyzje, które wspierają efektywne zarządzanie zasobami.
Jak obliczyć zapas maksymalny?
Obliczanie zapasów maksymalnych to najważniejszy element skutecznego zarządzania magazynem. Proces ten wymaga uwzględnienia wielu istotnych czynników, takich jak:
- dostępny kapitał – określa, ile środków można przeznaczyć na zakup i przechowywanie towarów,
- tempo konsumpcji – pozwala przewidzieć, jak szybko zapasy będą zużywane,
- pojemność magazynu – ogranicza maksymalną ilość przechowywanych produktów,
- ryzyko przeterminowania produktów – szczególnie istotne w przypadku towarów o krótkim terminie ważności
Wszystkie te zmienne pomagają znaleźć równowagę między kosztami przechowywania a koniecznością zapewnienia ciągłości dostaw. Ciągłość dostaw jest fundamentem sprawnego funkcjonowania każdej firmy, dlatego tak ważne jest jej utrzymanie.
Wzór na zapas maksymalny
Jednym z najczęściej stosowanych narzędzi do obliczania zapasów maksymalnych jest formuła Wilsona, która pozwala określić optymalną wielkość zamówień oraz częstotliwość składania zamówień.
Formuła Wilsona uwzględnia trzy aspekty:
- koszty zamówienia – związane z realizacją każdego zamówienia,
- koszty przechowywania – wynikające z magazynowania towarów,
- poziom popytu – określający zapotrzebowanie na dany produkt.
Celem jest znalezienie takiej ilości zamówienia Q*, która zminimalizuje łączne koszty związane z zamówieniami (koszty zamawiania) i przechowywaniem zapasów (koszty magazynowania). Formuła ta zakłada, że zapotrzebowanie jest stałe w czasie, a także, że koszty związane z zamówieniami i magazynowaniem są liniowe.
Formuła Wilsona jest znana także jako EOQ (Economic Order Quantity). Model ten zakłada, że firma musi zamówić zapasy w odpowiednich ilościach, aby zminimalizować koszty związane z magazynowaniem, zamawianiem oraz brakami w zapasach.
Formuła Wilsona (EOQ) wygląda następująco:
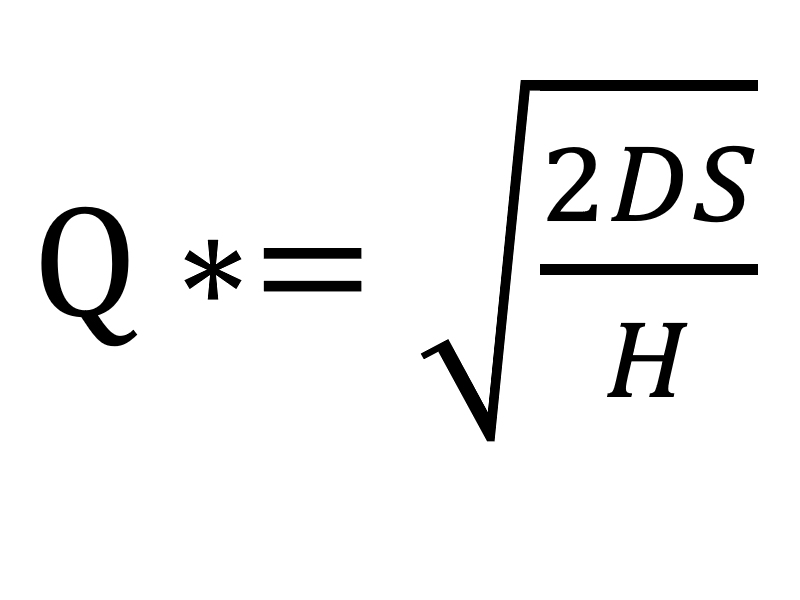
gdzie:
- Q* to optymalna ilość zamówienia (tzw. zapas maksymalny),
- D to roczne zapotrzebowanie na dany produkt (ilość sztuk),
- S to koszt zamówienia – jest to koszt związany z jednym zamówieniem, niezależnie od wielkości zamówienia (np. koszt transportu, obsługi zamówienia).
- H to koszt przechowywania jednostki zapasu przez rok (np. opłaty za przechowywanie, ubezpieczenie i inne koszty związane z zapasami
Przykład obliczeń zapasów maksymalnych
Aby lepiej zrozumieć, jak działa ten mechanizm, przyjrzyjmy się konkretnemu przykładowi. Wyobraź sobie firmę, która musi określić następujące parametry:
- punkt zamawiania – moment, w którym należy złożyć nowe zamówienie,
- wielkość uzupełnienia – ilość produktów, które należy zamówić,
- minimalny popyt – najniższe przewidywane zapotrzebowanie na produkt,
- czas realizacji zamówienia (lead time) – czas potrzebny na dostarczenie zamówienia.
Załóżmy, że firma ma roczne zapotrzebowanie na 10 000 jednostek danego produktu (D=10000), koszt zamówienia wynosi 50 zł (S=50) na jedno zamówienie, a koszt przechowywania jednej jednostki w magazynie to 2 zł rocznie (H=2).
Podstawiając te wartości do wzoru Wilsona:
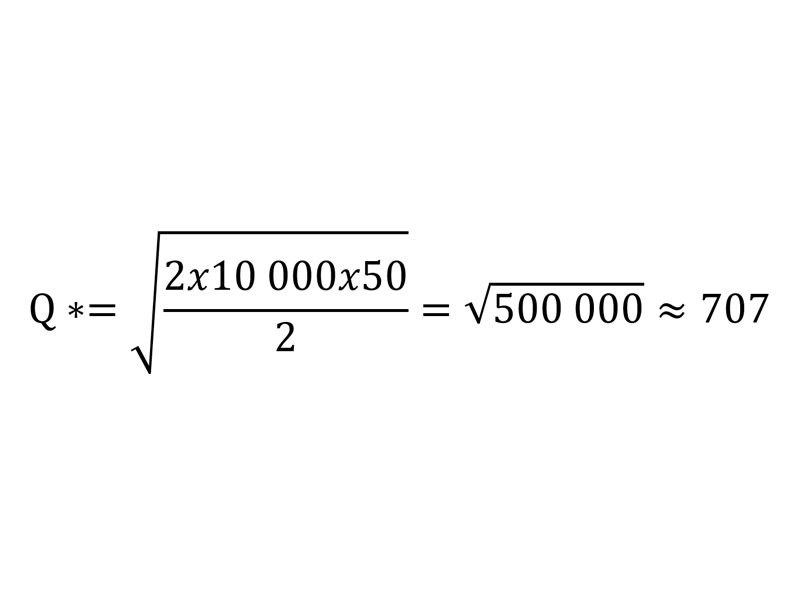
Optymalna wielkość zamówienia to 707 jednostek.
Rola systemu WMS w obliczaniu zapasów
Współczesne technologie, takie jak system WMS (Warehouse Management System), odgrywają kluczową rolę w zarządzaniu zapasami maksymalnymi. Tego rodzaju systemy automatyzują procesy magazynowe, wspierając kontrolę zapasów i organizację uzupełnień. Jakie korzyści przynoszą w praktyce?
- Stałe monitorowanie poziomów zapasów – pozwala na bieżąco kontrolować dostępność produktów.
- Optymalizacja wykorzystania przestrzeni magazynowej – efektywne zarządzanie miejscem w magazynie.
- Minimalizacja ryzyka przeterminowania produktów – szczególnie ważne w przypadku towarów o krótkim terminie ważności.
Automatyzacja tych procesów nie tylko zwiększa efektywność operacyjną, ale także pozwala szybciej reagować na zmieniające się potrzeby rynku. Dzięki temu firmy zyskują przewagę konkurencyjną, która jest kluczowa w dynamicznym środowisku biznesowym.
Optymalizacja zapasów maksymalnych
Skuteczne zarządzanie magazynem zaczyna się od optymalizacji poziomów zapasów maksymalnych. To proces, który pozwala precyzyjnie określić, ile towarów powinno znaleźć się w magazynie, aby z jednej strony ograniczyć koszty, a z drugiej – zminimalizować ryzyko operacyjne. Dzięki temu firmy mogą uniknąć zarówno braków, które mogłyby zakłócić dostawy, jak i nadmiaru, który generuje zbędne wydatki.
Optymalizacja ta uwzględnia wiele zmiennych, takich jak:
- zmienność popytu,
- czas realizacji zamówień (lead time),
- koszty przechowywania.
Analizując te czynniki, przedsiębiorstwa mogą lepiej przewidywać potrzeby i unikać sytuacji, które mogłyby prowadzić do przerw w produkcji lub sprzedaży. W efekcie zyskują przewagę konkurencyjną, utrzymując stabilność operacyjną nawet w obliczu nagłych zmian popytu.
Zapas maksymalny a zapas minimalny – jak utrzymać równowagę?
W zarządzaniu magazynem ważne jest znalezienie równowagi między zapasem maksymalnym a zapasem minimalnym. Pierwszy określa maksymalną ilość towarów, jaką można przechowywać, drugi – minimalny poziom, który zapewnia ciągłość dostaw i zapobiega brakowi produktów. Te dwa parametry są ze sobą ściśle powiązane i wspólnie tworzą fundament efektywnego zarządzania zapasami.
Precyzyjne ustalanie tych poziomów wymaga uwzględnienia takich czynników jak:
- sezonowość popytu,
- czas realizacji zamówień,
- koszty magazynowania.
Na przykład w branżach o dużej zmienności popytu, takich jak handel detaliczny, odpowiednie planowanie zapasów minimalnych i maksymalnych może znacząco wpłynąć na rentowność. Dzięki temu firmy unikają zarówno kosztów nadmiaru towarów, jak i strat wynikających z braków magazynowych. To przekłada się na lepsze zarządzanie zasobami i wyższą efektywność operacyjną.
Zapas zabezpieczający jako zawór bezpieczeństwa
W logistyce zapas zabezpieczający pełni rolę swoistej polisy ubezpieczeniowej. Chroni przed nieprzewidzianymi sytuacjami, takimi jak nagłe wzrosty popytu czy opóźnienia w dostawach. To dodatkowa ilość towarów, która zapewnia bufor bezpieczeństwa w kryzysowych momentach. Na przykład w branży farmaceutycznej zapas zabezpieczający może być kluczowy, by zapewnić dostępność leków w przypadku nieoczekiwanych problemów z dostawami.
Efektywne zarządzanie zapasem zabezpieczającym pozwala firmom:
- minimalizować ryzyko przerw w produkcji lub sprzedaży,
- zwiększać zadowolenie klientów,
- utrzymać swoją pozycję na rynku.
Wdrożenie odpowiednich procedur zarządzania zapasem zabezpieczającym to inwestycja w stabilność operacyjną i długoterminowy rozwój.
Konsekwencje przekroczenia zapasów maksymalnych
Przekroczenie zapasów maksymalnych może prowadzić do poważnych konsekwencji zarówno w obszarze operacyjnym, jak i finansowym. Jednym z problemów jest powstawanie nadmiernych zapasów, które generują dodatkowe koszty magazynowania. To zmusza firmy do ciągłego monitorowania stanów magazynowych, aby unikać zbędnych wydatków i zachować płynność operacyjną. Każda firma dąży przecież do optymalizacji swoich zasobów, co czyni ten proces kluczowym dla jej funkcjonowania.
Zapas nadmierny – przyczyny i skutki
Nadmierne zapasy to sytuacja, w której ilość zgromadzonych towarów znacząco przewyższa rzeczywiste potrzeby przedsiębiorstwa. Taki stan nie tylko podnosi koszty magazynowania, ale także zwiększa ryzyko utraty wartości produktów, szczególnie w przypadku towarów o krótkim terminie przydatności. Przekroczenie zapasów maksymalnych jest głównym źródłem tego problemu, co wymaga od firm precyzyjnego planowania i efektywnego zarządzania zasobami.
W branży spożywczej na przykład nadmiar produktów może prowadzić do ich przeterminowania, co oznacza nie tylko straty finansowe, ale także potencjalne szkody wizerunkowe. Tego rodzaju sytuacje mogą negatywnie wpłynąć na zaufanie klientów do marki, co czyni zarządzanie zapasami jeszcze bardziej istotnym.
Ryzyko nadmiernych kosztów przechowywania
Jednym z najpoważniejszych wyzwań związanych z nadmiarem zapasów jest rosnący koszt przechowywania. Zbyt duże ilości towarów oznaczają wyższe wydatki na:
- wynajem przestrzeni magazynowej,
- zużycie energii,
- wynagrodzenia dla pracowników,
- utrzymanie infrastruktury magazynowej.
Firma, która nie dostosowuje poziomu zapasów do sezonowych wahań popytu, może niepotrzebnie ponosić koszty utrzymania nadmiaru towarów. Regularne analizowanie potrzeb magazynowych i optymalizacja poziomów zapasów pozwalają uniknąć zbędnych wydatków oraz poprawić efektywność operacyjną. Każda oszczędność w tym obszarze to krok w stronę większej konkurencyjności na rynku.
Jak uniknąć problemów z nadmiarem zapasów?
Aby skutecznie zapobiegać problemom wynikającym z nadmiaru zapasów, przedsiębiorstwa powinny wdrożyć następujące działania:
- regularne monitorowanie stanów magazynowych i dostosowywanie ich do zmieniającego się popytu, co pozwala szybko reagować na potrzeby rynku.
- inwestycja w nowoczesne systemy zarządzania magazynem takie jak oprogramowanie ERP automatyzuje procesy i umożliwia precyzyjną kontrolę zapasów.
- lepsze planowanie zamówień, które minimalizuje ryzyko nadmiaru towarów i pozwala na efektywniejsze zarządzanie zasobami.
Dzięki tym strategiom firmy mogą nie tylko ograniczyć koszty magazynowania, ale także zwiększyć swoją konkurencyjność na rynku.
Praktyczne aspekty zarządzania zapasami maksymalnymi
Efektywne zarządzanie zapasami maksymalnymi to najważniejszy element sukcesu w logistyce i zarządzaniu magazynem. Wymaga ono uwzględnienia trzech głównych obszarów:
- analiza popytu pozwalająca zrozumieć, które produkty są najbardziej pożądane przez klientów i w jakich ilościach. Analiza popytu pozwala firmom precyzyjnie określić, ile towarów powinno znaleźć się w magazynie, aby zaspokoić potrzeby rynku, jednocześnie unikając zbędnych wydatków.
- optymalizacja zapasów umożliwiająca dostosowanie poziomu zapasów do aktualnych potrzeb, bez ponoszenia nadmiernych kosztów magazynowania.
- harmonijna współpraca z dostawcami zapewniająca płynność dostaw i możliwość negocjowania korzystniejszych warunków zakupu.
Proces ustalania zapasów maksymalnych
Proces ustalania zapasów maksymalnych wymaga uwzględnienia wielu zmiennych, takich jak:
- rotacja zapasów – tempo sprzedaży lub zużycia produktów w określonym czasie. Wysoka rotacja oznacza konieczność utrzymywania większych zapasów, natomiast niska rotacja sugeruje ograniczenie ich poziomu.
- sezonowość – w okresach wzmożonego popytu, takich jak święta czy promocje, firmy muszą zwiększyć zapasy, aby sprostać oczekiwaniom klientów.
Zrozumienie tych czynników pozwala lepiej planować i efektywniej zarządzać zasobami magazynowymi. W efekcie firmy mogą osiągnąć większą satysfakcję klientów oraz lepsze wyniki finansowe.
Monitorowanie rotacji zapasów i zapasów bieżących
Regularne monitorowanie rotacji zapasów oraz zapasów bieżących to fundament skutecznego zarządzania magazynem. Dzięki temu firmy mogą:
- dostosowywać poziomy zapasów maksymalnych do zmieniających się potrzeb rynku,
- unikać zarówno braków, jak i nadmiaru towarów, co poprawia efektywność operacyjną,
- zminimalizować koszty związane z przechowywaniem nadwyżki towarów.
Zapas bieżący, czyli aktualna ilość towarów dostępnych w magazynie, powinien być stale porównywany z zapasem maksymalnym. Taka analiza umożliwia lepsze planowanie zamówień i zapewnia płynność operacyjną, co przekłada się na wysoki poziom obsługi klienta.
Wykorzystanie zapasów sezonowych i rezerwowych
Strategiczne podejście do zapasów sezonowych oraz rezerwowych również jest konieczne dla efektywnego zarządzania magazynem:
- zapas sezonowy – przechowywany przed okresem wzmożonego popytu, takim jak święta czy wyprzedaże, pozwala uniknąć braków towarów w kluczowych momentach,
- zapas rezerwowy – pełni rolę bufora na wypadek nieprzewidzianych sytuacji, takich jak nagłe wzrosty popytu czy opóźnienia w dostawach.
Uwzględnienie tych rodzajów zapasów w planowaniu zapasów maksymalnych pozwala firmom lepiej zarządzać ryzykiem i zapewnić ciągłość dostaw. Odpowiednie wykorzystanie zapasów sezonowych i rezerwowych to zapewnienie stabilności operacyjnej oraz zadowolenia klientów.
Znaczenie zapasów maksymalnych w logistyce – podsumowanie
Efektywne zarządzanie zapasami maksymalnymi to fundament sprawnego funkcjonowania każdej firmy. Dzięki nim przedsiębiorstwa mogą utrzymać płynność operacyjną i spełniać oczekiwania swoich klientów. Odpowiednie określenie tych zapasów pozwala znaleźć równowagę między kosztami magazynowania a ciągłością dostaw. Co to oznacza w praktyce? Unikniesz zarówno pustych półek, jak i przepełnionych magazynów. W rezultacie Twoja firma będzie lepiej przygotowana na dynamiczne zmiany rynkowe, co przełoży się na przewagę konkurencyjną.
Jak widać, warto postawić na optymalizację zapasów maksymalnych, aby zwiększyć efektywność operacyjną i poprawić satysfakcję klientów. Rynek zmienia się w zawrotnym tempie, więc dostosowanie strategii zarządzania zapasami do aktualnych trendów to konieczność.
Strategia | Korzyści |
Inwestycje w nowoczesne technologie | Precyzyjne monitorowanie stanów magazynowych i szybka reakcja na zmiany. |
Zaawansowane systemy zarządzania magazynem | Lepsza organizacja i optymalizacja procesów magazynowych. |
Współpraca z dostawcami | Lepsze planowanie dostaw i unikanie opóźnień. |
Wdrożenie tych strategii nie tylko obniży koszty operacyjne, ale także wzmocni pozycję firmy na rynku. Stanie się atrakcyjniejszym partnerem biznesowym budując długoterminowe relacje.