5 najczęstszych błędów w projektowaniu magazynu i jak ich uniknąć
Projektowanie magazynu to pojęcie, które swoim zakresem obejmuje wiele zagadnień – od projektowania architektonicznego, po integrację automatyki i digitalizację obiektu. Wszystkie te obszary wymagają odpowiedniego przygotowania, oszacowania zasobów i możliwości rozwojowych oraz strategicznego podejścia. Niestety, w praktyce często powielane są te same błędy, które mogą skutecznie zakłócić codzienne funkcjonowanie magazynu.
Jako firma dostarczająca wyposażenie techniczne, w tym artykule chcielibyśmy skoncentrować się na błędach wynikających z niewłaściwie zaprojektowanych procesów. Postaramy się również wskazać, jak uniknąć 5 – według nas – najczęstszych błędów w projektowaniu magazynu. Zapraszamy do lektury!
1. Błędy w planowaniu przestrzeni i przepływu materiałów
Brak analizy przepływu materiałów i logicznego układu przestrzennego
To jeden z najczęstszych i najbardziej kosztownych błędów popełnianych przy projektowaniu magazynu. Zaskakująco często przestrzeń jest planowana „na oko”, bez dokładnego prześledzenia, jak faktycznie poruszają się towary i ludzie. Efekt em jest chaos organizacyjny, przestoje, niepotrzebne kilometry pokonywane przez pracowników i ogólne marnotrawstwo czasu oraz energii.
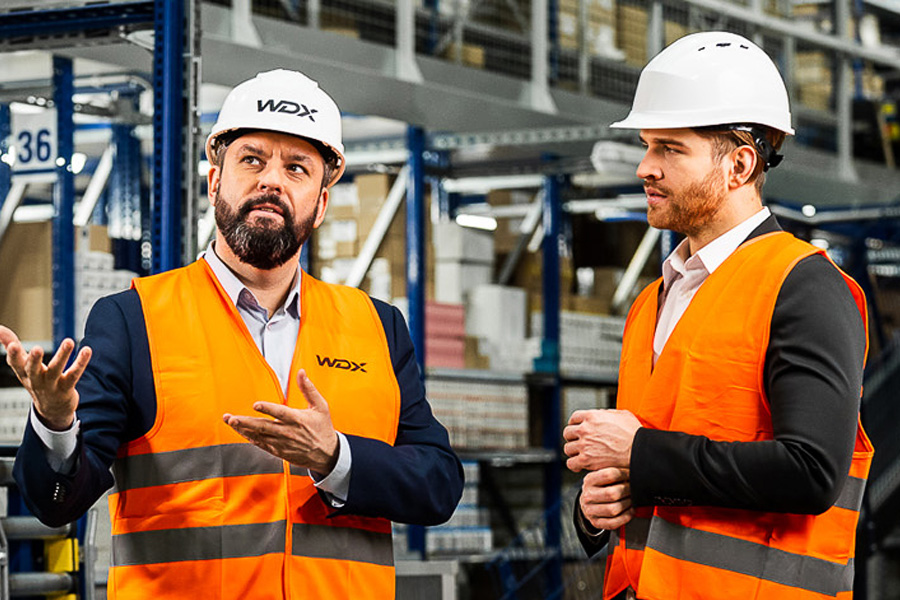
Klasyczny przykład: strefa przyjęcia towaru znajduje się na jednym końcu hali, a kompletacja zamówień na drugim. Wydaje się, że to drobiazg, ale w praktyce oznacza dziesiątki, a często setki metrów do pokonania przy każdym cyklu pracy. Im więcej takich nieprzemyślanych rozwiązań, tym bardziej cierpi cała logistyka: procesy zwalniają, rosną koszty operacyjne, a klienci czekają dłużej na swoje zamówienia.
Czytaj na naszym blogu: Podział magazynu na strefy
Dlatego analiza przepływu materiałów powinna być pierwszym krokiem przy projektowaniu magazynu. Warto dokładnie prześledzić, skąd i dokąd przemieszczają się towary, jak często to się dzieje, i kto bierze w tym udział. Układ przestrzenny powinien być logiczny i oparty na danych, a nie przypadkowy. Dobrze zaprojektowana przestrzeń pozwala nie tylko na sprawną realizację bieżących operacji, ale też na łatwe skalowanie działalności w przyszłości.
Zanim cokolwiek ustawisz w magazynie, najpierw zastanów się, którędy ma iść towar, a dopiero potem, którędy mają chodzić ludzie.
Nieefektywne wykorzystanie przestrzeni magazynowej
Wielu menedżerów nie zdaje sobie sprawy, ile przestrzeni w magazynie się marnuje, dopóki nie zrobi się naprawdę ciasno. Zbyt szerokie alejki, niewykorzystana wysokość hali, chaotycznie rozmieszczone regały, wszystko to ogranicza wydajność operacyjną. Odpowiednia organizacja przestrzeni magazynowej może zwiększyć jej pojemność nawet o kilkadziesiąt procent bez konieczności rozbudowy czy przeprowadzki.
Jak to osiągnąć? Warto wdrożyć rozwiązania, które maksymalizują wykorzystanie dostępnej powierzchni:
- regały wysokiego składowania – pozwalają efektywnie wykorzystać wysokość hali,
- automatyczne systemy magazynowe – zwiększają szybkość i precyzję operacji,
- optymalizacja stref i tras transportowych – skraca czas przemieszczania się towarów i pracowników.
2. Brak elastyczności i skalowalności magazynu
Magazyn to nie tylko miejsce przechowywania. To centrum operacyjne, które może napędzać rozwój firmy lub skutecznie go hamować. Niestety, najczęstsze błędy w planowaniu przestrzeni i procesów magazynowych potrafią zniweczyć nawet najlepsze intencje. Do najpoważniejszych problemów należą:
- brak elastyczności – uniemożliwia szybkie dostosowanie się do zmian rynkowych,
- trudności adaptacyjne – prowadzą do stagnacji i wzrostu kosztów operacyjnych.
- źle zaprojektowana przestrzeń – komplikuje codzienną pracę i ogranicza potencjał rozwoju.
Złe planowanie magazynu ogranicza skalowalność
Bez przemyślanej strategii magazyn szybko przestaje być wsparciem, a staje się przeszkodą. Brak miejsca na nowe produkty, wzrost zamówień czy sezonowe skoki sprzedaży mogą wywołać chaos organizacyjny. Skalowalność to obowiązek. Już na etapie projektowania magazynu należy myśleć przyszłościowo, nie tylko o obecnych potrzebach, ale i o tym, co może się wydarzyć za rok czy dwa.
Automatyzacja magazynowa jako sposób na zwiększenie efektywności
Wdrożenie nowoczesnych technologii pozwala zautomatyzować powtarzalne czynności, które wcześniej wymagały zaangażowania pracowników. Do najczęściej wykorzystywanych rozwiązań należą:
- AGV (Automated Guided Vehicles) – pojazdy sterowane automatycznie, transportujące towary wewnątrz magazynu,
- AMR (Autonomous Mobile Robots) – autonomiczne roboty mobilne, które samodzielnie poruszają się po magazynie,
- AS/RS (Automated Storage and Retrieval Systems) – zautomatyzowane systemy składowania i pobierania towarów.
W naszej ofercie znajdziesz autonomiczne wózki samojezdne AGV i roboty AMR.
Efekty wdrożenia automatyzacji są wymierne. Roboty mobilne mogą skrócić czas realizacji zamówień nawet o 50%, a ryzyko błędów ludzkich spada niemal do zera. Warto jednak pamiętać, że automatyzacja to nie tylko sprzęt. To również zmiana podejścia i gotowość do wdrażania innowacji.
Szkolenie personelu magazynowego w zakresie procedur i technologii
Szkolenia pracowników magazynowych – obejmujące regularne kursy i warsztaty z zakresu procedur oraz obsługi nowoczesnych narzędzi – to fundament skutecznego wdrożenia i działania systemów logistycznych. W szczególności warto zadbać o:
- obsługę interfejsu WMS – znajomość systemu zarządzania magazynem,
- korzystanie ze skanerów RFID – szybka identyfikacja i śledzenie towarów,
- zrozumienie zasad działania zautomatyzowanych systemów – efektywna współpraca z technologią.
Inwestycja w rozwój kompetencji to strategia, która przynosi wymierne korzyści – zarówno w krótkim, jak i długim okresie.
Wybór modułowych komponentów transportowych dla elastyczności systemu
Wdrożenie modułowych rozwiązań transportowych to sposób na stworzenie elastycznego i skalowalnego systemu magazynowego, który można łatwo dostosować do zmieniających się potrzeb biznesowych. Korzyści z zastosowania modułowości obejmują:
- łatwą rozbudowę infrastruktury – możliwość dodawania nowych komponentów w miarę rozwoju firmy,
- minimalizację kosztów modernizacji – brak konieczności przebudowy całego systemu,
- szybką adaptację do zmian rynkowych – elastyczność w reagowaniu na nowe wyzwania,
- zwiększenie odporności operacyjnej – lepsze przygotowanie na nieprzewidziane sytuacje.
3. Zaniedbania w zakresie technologii i systemów informatycznych
Niedopasowanie technologii i systemów
Niedopasowanie technologii może sparaliżować cały proces magazynowania. Gdy konkurencja wdraża nowoczesne rozwiązania, a Twoja firma wciąż opiera się na przestarzałych systemach, efektywność operacyjna drastycznie spada.
Brak integracji z systemami informatycznymi ogranicza kontrolę
Brak integracji między tymi systemami prowadzi do chaosu informacyjnego, ograniczonej kontroli i ryzyka zakłóceń w całym łańcuchu dostaw.
Typowy problem w wielu firmach to niewspółpracujące ze sobą systemy informatyczne. Gdy WMS, ERP i MES działają niezależnie, pojawiają się nieścisłości w danych, które prowadzą do błędnych decyzji.
Sprawdź nas wpis dotyczący integracji systemu WMS z ERP: https://wdx.pl/blog/integracja-wms-z-erp-realne-korzysci-i-pulapki-o-ktorych-warto-wiedziec/
Jeśli informacje o stanach magazynowych nie są automatycznie przekazywane do systemu ERP, może dojść do sytuacji, w której:
- zamówisz towar, który już znajduje się w magazynie,
- nie zamówisz brakującego asortymentu,
- powstaną nadwyżki zapasów,
- dojdzie do opóźnień w realizacji zamówień.
Opór przed automatyzacją hamuje rozwój operacyjny
Wiele firm nadal podchodzi do automatyzacji z rezerwą, co skutecznie ogranicza ich rozwój. Zautomatyzowane systemy nie tylko przyspieszają procesy, ale też znacząco redukują ryzyko błędów ludzkich.
Wdrożenie systemu WMS dla lepszego zarządzania zapasami
Wprowadzenie systemu WMS to krok w kierunku zwiększenia efektywności zarządzania zapasami oraz usprawnienia pracy magazynu. Dzięki niemu zyskujesz dostęp do aktualnych danych w czasie rzeczywistym dotyczących stanów magazynowych, lokalizacji towarów i przebiegu procesów. System WMS automatyzuje kluczowe operacje, co przekłada się na większą precyzję, szybkość i porządek w codziennym funkcjonowaniu magazynu. Co więcej, integracja WMS z systemami ERP czy TMS umożliwia pełną kontrolę nad całym łańcuchem dostaw od momentu przyjęcia towaru aż po jego wysyłkę.
4. Problemy z zarządzaniem zapasami
Efektywne zarządzanie magazynem to podstawa sprawnego działania każdej firmy. Niestety, wiele przedsiębiorstw wciąż boryka się z powtarzającymi się problemami w tym obszarze. Warto przyjrzeć się najczęstszym przyczynom tych trudności, bo jak pokazuje praktyka, to właśnie detale decydują o sukcesie lub porażce.
Niedokładne śledzenie zapasów powoduje błędy operacyjne
Jednym z najczęstszych problemów jest niedokładne śledzenie stanów magazynowych. Gdy dane w systemie nie odpowiadają rzeczywistości, pojawiają się liczne komplikacje, a wystarczy zadbać o rzetelną ewidencję, by uniknąć takich wpadek.
Brak wiedzy o lokalizacji towarów utrudnia kompletację
Nieprecyzyjna informacja o położeniu produktów w magazynie prowadzi do chaosu. Pracownicy tracą czas na poszukiwania, a proces kompletacji zamówień wydłuża się. Problem ten szczególnie dotyczy firm, które nie korzystają z nowoczesnych systemów WMS.
Zduplikowane kartoteki towarowe zaburzają ewidencję
Duplikaty kartotek towarowych to ukryty problem, który może poważnie zakłócić pracę magazynu. Gdy ten sam produkt występuje w systemie pod różnymi nazwami lub kodami, pojawiają się trudności, obejmujące: błędy przy zamówieniach, problemy z inwentaryzacją czy nieefektywne zakupy. Rozwiązaniem są systemy WMS z funkcją integracji kodów kreskowych, które automatycznie wykrywają i eliminują duplikaty.
Brak śledzenia dat ważności produktów zwiększa ryzyko strat
W przypadku produktów z określoną datą przydatności brak kontroli terminów ważności może prowadzić do poważnych strat. Systemy WMS oferują funkcje, które pomagają w zarządzaniu terminami:
- monitorowanie dat ważności – system automatycznie ostrzega o zbliżającym się terminie,
- wsparcie dla zasady FIFO (first in, first out) – najstarsze produkty są wydawane jako pierwsze,
- redukcja strat magazynowych – nawet o 40% w branży spożywczej.
Niewłaściwy dobór komponentów systemu wpływa na niezawodność
Nie tylko oprogramowanie decyduje o sukcesie systemu magazynowego. Równie ważne są fizyczne komponenty, takie jak skanery, przenośniki czy systemy transportowe. Inwestycja w sprawdzone i kompatybilne rozwiązania to gwarancja stabilności, mniejszego stresu i możliwość skalowania systemu wraz z rozwojem firmy. Zamiast gasić pożary, lepiej budować solidne fundamenty na przyszłość.
Brak analizy danych magazynowych utrudnia optymalizację
W dobie cyfryzacji ignorowanie danych to kosztowny błąd. Bez wglądu w informacje z magazynu trudno dostrzec słabe punkty, zminimalizować marnotrawstwo zasobów i wdrożyć skuteczne usprawnienia. Wdrożenie narzędzi analitycznych pozwala na:
- monitorowanie procesów w czasie rzeczywistym,
- szybkie reagowanie na pojawiające się problemy,
- podejmowanie decyzji opartych na twardych danych,
- ciągłą optymalizację działań.
5. Błędy w organizacji pracy, bezpieczeństwie i zarządzaniu personelem
Zaniedbania w zakresie bezpieczeństwa i ergonomii
Bezpieczeństwo i ergonomia w magazynie to fundamenty efektywnej pracy. Ich ignorowanie może prowadzić do poważnych incydentów, obniżenia komfortu oraz spadku motywacji pracowników. Nikt nie chce pracować w stresujących i niewygodnych warunkach. W tej części przyjrzymy się, co może pójść nie tak, gdy zasady BHP są lekceważone, ergonomia traktowana po macoszemu, a sprzęt nie przechodzi regularnych przeglądów. Skutki takich zaniedbań bywają znacznie poważniejsze niż się wydaje.
Nieprzestrzeganie procedur bezpieczeństwa zwiększa ryzyko wypadków
Magazyn to dynamiczne i pełne wyzwań środowisko. Wózki widłowe, palety, hałas i ludzie w ciągłym ruchu sprawiają, że każda nieuwaga może skończyć się wypadkiem. Wystarczy chwila zapomnienia, źle zabezpieczony ładunek lub brak odpowiedniego obuwia, by doszło do tragedii. Wypadki w magazynie mogą prowadzić do poważnych konsekwencji, takich jak zagrożenie zdrowia i życia pracowników, dezorganizacja pracy i przestoje oraz spadek morale w zespole. Dlatego tak ważne jest, by regularnie przypominać o procedurach BHP, organizować szkolenia oraz budować kulturę odpowiedzialności i zaufania wśród pracowników. Pamiętaj, że bezpieczeństwo to proces, który wymaga zaangażowania całego zespołu, a nie jednorazowej interwencji.
Sprawdź: Jak dbać o bezpieczeństwo w przestrzeni magazynowej?
Zaniedbanie ergonomii i oznakowania obniża komfort pracy
Brak odpowiednich rozwiązań, takich jak ergonomiczne stanowiska czy czytelne oznakowanie, prowadzi do chronicznego zmęczenia, bólu pleców, urazów związanych z niewłaściwym podnoszeniem ciężarów oraz obniżenia efektywności i motywacji pracowników.
Ważnym aspektem jest także odpowiednie oznakowanie przestrzeni magazynowej. Brak widocznych tablic informacyjnych lub ich nieprawidłowe rozmieszczenie wprowadza chaos i prowadzi do błędów, które w skrajnych przypadkach mogą stanowić zagrożenie zdrowia i życia.
Brak konserwacji sprzętu magazynowego prowadzi do awarii
Sprzęt magazynowy, taki jak wózki widłowe, regały czy systemy transportowe, musi działać niezawodnie. Ignorowanie konieczności regularnych przeglądów technicznych wiąże się z ryzykiem poważnych awarii. Skutki zaniedbania to nie tylko nieplanowane przestoje w pracy, ale także wzrost ryzyka wypadków i uszkodzeń towaru oraz wyższe koszty napraw i ewentualnych odszkodowań.
Aby uniknąć takich sytuacji, niezbędne jest przestrzeganie harmonogramu konserwacji. Regularne przeglądy, dokumentacja stanu technicznego oraz szkolenie pracowników z zakresu obsługi i zgłaszania usterek to klucz do utrzymania sprzętu w dobrym stanie i zapewnienia ciągłości pracy.
Brak szkoleń i rozwoju personelu zwiększa rotację
Wiele firm logistycznych popełnia błąd, ignorując konieczność szkoleń i rozwoju pracowników. W magazynach, gdzie liczy się zarówno precyzja, jak i tempo, brak odpowiedniego przygotowania prowadzi do popełniania błędów operacyjnych, narastającej frustracji, spadku motywacji oraz wysokiej rotacji pracowników.
Niespójne procesy kompletacji powodują opóźnienia
Brak jednolitych, jasno określonych procedur kompletacji prowadzi do chaosu i nieefektywności. Pracownicy nie wiedzą, jak działać, a nieoptymalne trasy powodują opóźnienia w realizacji zamówień, błędy przy kompletacji oraz spadek satysfakcji klientów.
Błędy organizacyjne i kadrowe
W logistyce, gdzie dynamika pracy jest niezwykle wysoka, nawet drobne błędy organizacyjne czy kadrowe mogą prowadzić do poważnych problemów. Niezgodności w tym obszarze powodują wysoką rotację pracowników, co obniża wydajność i narusza spójność zespołu. Brak inwestycji w rozwój personelu oraz nieskoordynowane procesy kompletacji mogą osłabić funkcjonowanie magazynu.
Podsumowanie
Kiedy brakuje dobrego planu i wszystko jest robione na szybko i po omacku, zaczynają się problemy: zamówienia idą wolniej, pojawiają się błędy, a koszty rosną. Często zapomina się o tym, żeby dobrze przeanalizować, jak to wszystko powinno się poruszać i jak poukładać przestrzeń.
Na szczęście dziś jest mnóstwo narzędzi i technologii, które pomagają to wszystko uporządkować – systemy WMS, automatyczne regały, roboty i inteligentne programy. Dzięki nim można lepiej wykorzystać miejsce, szybciej realizować zamówienia i unikać błędów.
Ale nawet najlepsza technologia nie zastąpi dobrze przeszkolonych ludzi i przemyślanych działań. Dlatego warto inwestować w rozwój pracowników i stawiać na systematyczność. Wtedy magazyn działa sprawnie, firma nie traci czasu i pieniędzy, a klienci są zadowoleni.